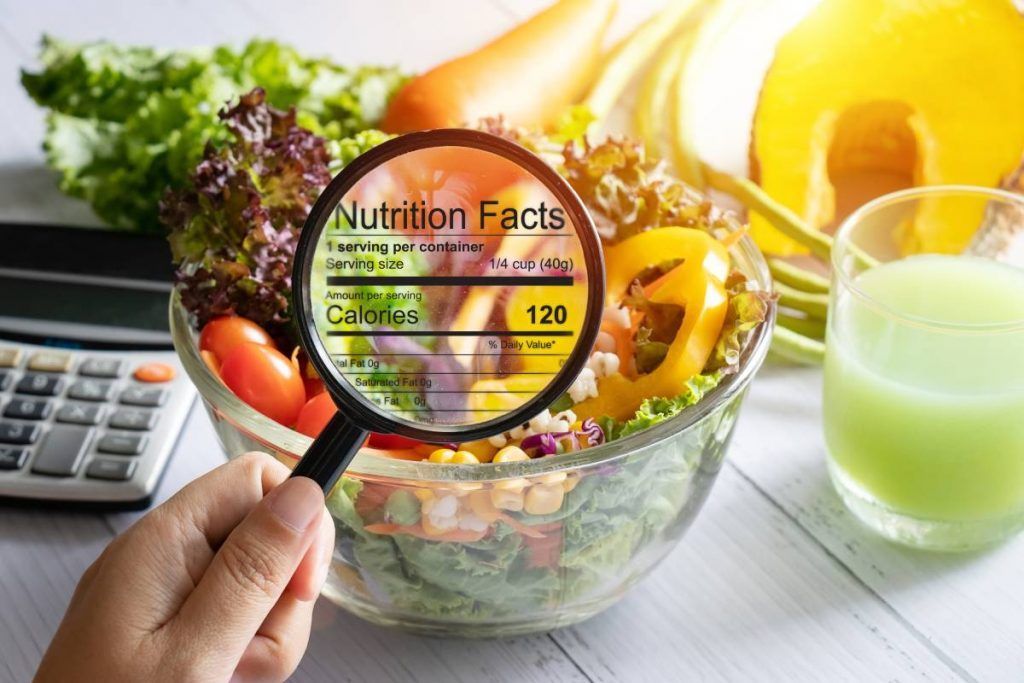
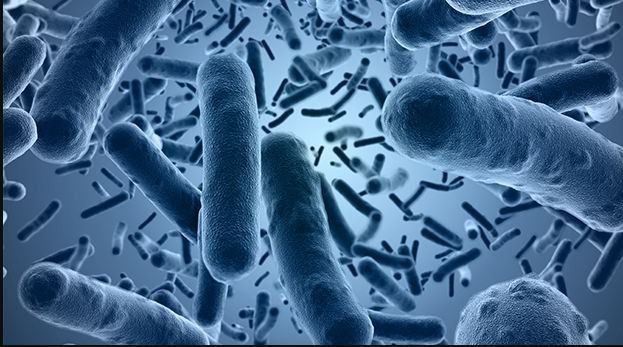
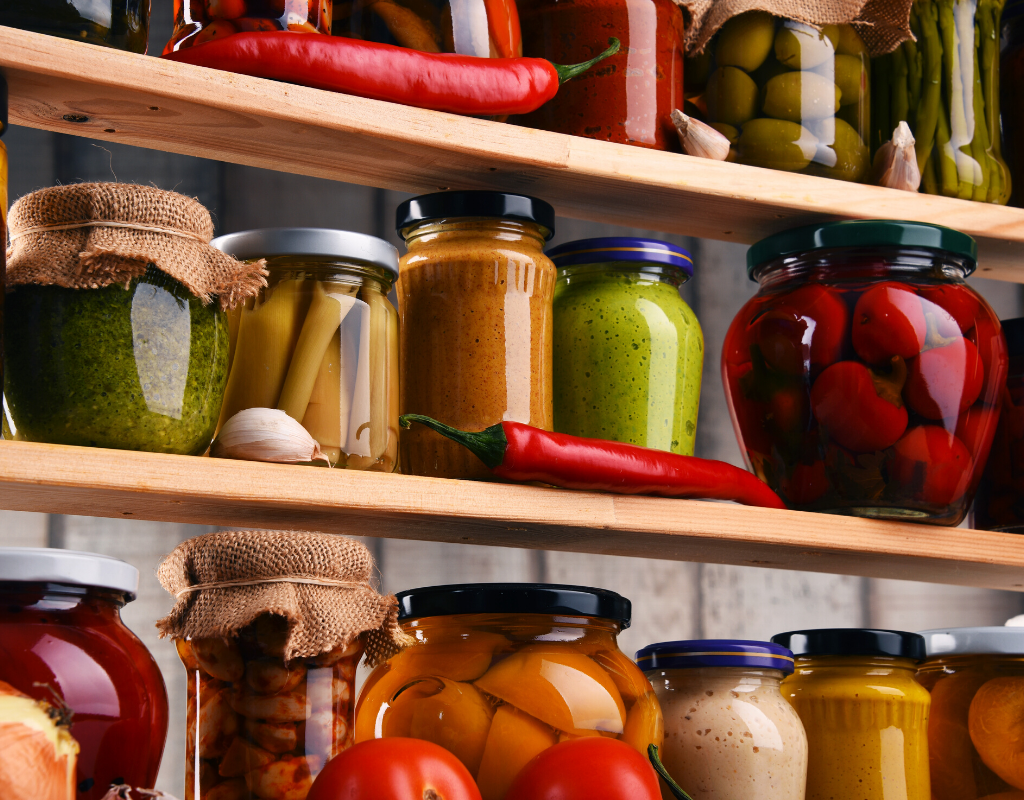
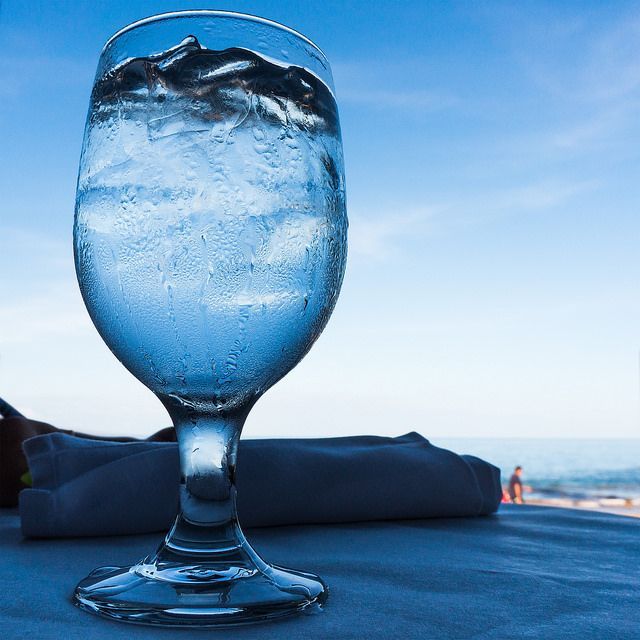
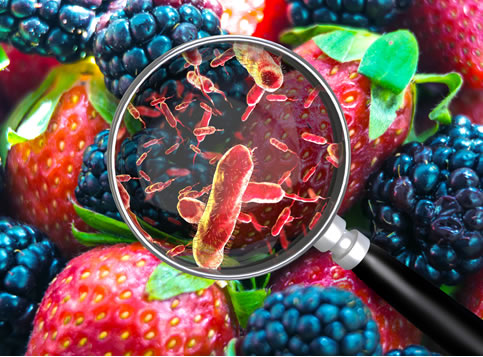
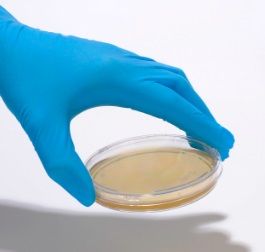
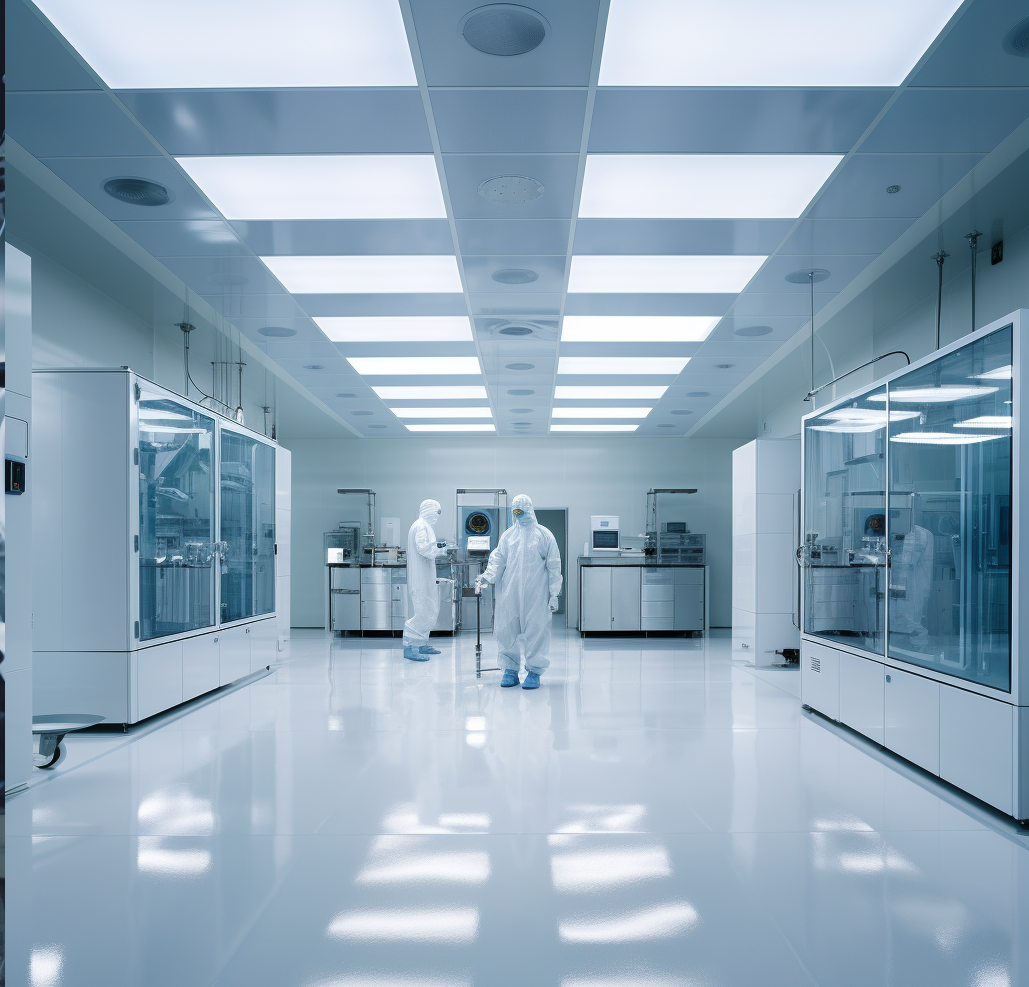
USP stands for the United States Pharmacopeia. USP testing is used to monitor sterility conditions. By testing for bioburden and endotoxins. USP 797 standards are typically developed for the purposes of standardizing product quality, making items bought at the store both predictable (the consumer knows what they are getting) and safer.
USP 797 guidelines 2022 can be somewhat difficult for the layperson to understand.
With professional guidance and the right knowledge, it is easy to maintain regulated standards. In this article, we go over everything you need to know about USP 797.
According to USP, "millions of medications are compounded each year in the US to meet the unique needs of patients." USP 797 is a pharmaceutical standard designed to prevent patient death or harm through lax developmental processes. By monitoring pharmaceutical development USP 797 standards ensure that consumers know exactly what they are getting when they fill out a prescription.
This is accomplished by routinely examining employee behavior, testing equipment, and testing workstations and other often touched surfaces to detect contamination.
Personnel Tests are typically taken at the end of a work cycle. For example, a glove tip test (more on that later) may be performed at the end of the shift, to find out before sanitation processes begin if there is evidence of microbial contamination.
USP 797 applies to everyone involved in compound sterile preparations (CSPs). CSPs refer to all the individuals and locations involved in the development and distribution of pharmaceuticals, including pharmacists, physicians, nurses, and technicians.
All of these people are guided directly by USP 797, beholden to its standards in how they handle and interact with medications destined for patient consumption. Through strict training and careful guideline adherence, these pillars of the healthcare system can help ensure both their own safety and public safety.
USP 797 sets compounding risk levels based on the odds of contamination. This is done to set guidelines that are specific to the unique circumstances that go into pharmaceutical distribution. USP 797 includes guidance on air quality standards, microbial surface contamination, and human contamination. These factors combine to determine risk levels and guide behavior.
USP 797 protects patients and pharmacists alike. The standards pertain to any environments involved in compound sterile preparations. This includes everything from hospitals to retail environments.
Patients get the medication that they need. Pharmacists are guaranteed a work environment with minimal personal risk factors.
At a glance, the risk levels defined by USP 797 are very straightforward: low, medium, and high. The factors that contribute to each risk category can be slightly harder to follow.
Low refers to single-dose sterile ingredients that are not likely to produce notable levels of air contamination.
Medium risk refers to sterile doses that are to be administered either to multiple patients or to one patient multiple times.
High risk involves either non-sterile ingredients or conditions that could involve compromised air quality.
These risk levels are used, in part to establish how often surface and employee testing must be performed. Low-risk environments may only need to perform certain tests on an annual basis, while higher-risk environments will have to do them more often.
USP 797 outlines policies and procedures that are designed to ensure both drug and patient safety. Though stringent, these rules are there as a safeguard to catch contamination issues at the earliest possible stage.
USP 797 regulations put a big emphasis on staff training for the simple reason that any other standard can be compromised through human error. For these guidelines to truly be effective, everyone working on the staff needs to be on the same page.
A well-trained staff understands how to avoid bringing contaminants into the work environment, while also understanding how to properly sanitize and maintain their stations.
Most organizations and labs have their own set of guidelines and standards. Fore example, American Academy of Allergy Asthma & Immunology requires that "all compounding personnel must complete training and be able to demonstrate knowledge of theoretical principles and skills for sterile compounding. Personnel must demonstrate proficiency in these procedures by passing written or electronic testing before being allowed to compound allergenic extract prescription sets."
Many sterility guidelines are straightforward and include relatively simple concepts like using sterile gloves, eliminating personal attire in favor of sterilized garments, making training an ongoing effort, and performing us to make sure that conditions haven’t lapsed.
Though these guidelines are easy to follow, they are often why lapses take place. Employees forget something or cut a corner to expedite a process. Businesses wishing to avoid the big messes that can stem from small mistakes should make training an ongoing priority.
Incoming employees are screened for hygienic competency and required to pass several stages of tests before they can be considered fully onboarded. While this is important, it’s also vital to continue training and refreshing existing employees on ideal practices.
Of course, staff can only bear so much of the burden. Even strict adherence to 797 guidelines isn’t enough to guarantee lab purity at the microbial level without the right environmental infrastructure.
Air quality and surface cleanliness must be constantly maintained and monitored. Even brief lapses can create conditions that are deemed unsafe. Ideal conditions can only be monitored and maintained through routine testing. It’s important to remember that contamination and lapses can are rarely detectable by the human eye. Testing gives you information that would otherwise be impossible to get on your own.
Air monitoring is a vital component of maintaining 797 standards—many of which directly hinge on securing certain levels of air purity. Microbial contaminants can easily hang in the air of a room that, by ordinary standards would be considered clean. From a cleanroom standard, however, these conditions are dangerous and unacceptable.
Similarly, physical surfaces must also be routinely monitored for contamination. This can be done using periodic tests and contact plates to guarantee that ideal conditions are being maintained.
Because microbial contamination can occur in a split second, routine testing is vital to making sure conditions remain ideal.
As mentioned earlier, people will make mistakes periodically. Errors that would usually be considered minor—using a glove that isn’t properly sterile—can have enormous repercussions based on the strict standards of USP 797.
You can avoid these mistakes by routinely training and testing your staff on proper guidelines. The goal is not to police team members, but to equip them with the training and knowledge they need to keep themselves, and your customers safe.
Glove tip sampling tests for fungal and bacterial infection. There is an initial round of testing, for which the ideal results are zero registered contaminants. After that, comes re-evaluation sampling. For this round, media-fill testing has been completed and the standard dictates a reading of <3CFU as the ideal.
Initial employee testing standardizes competency. Essentially, it’s there to make sure that incoming staff members will be able to complete the necessary hygienic procedures required to maintain 797 standards.
To perform initial employee testing, incoming workers replicate hygienic procedures three times for each hand. The objective is to make sure these employees understand the hygienic process, and that they will have the skills required to execute it every day without fail.
Employee re-evaluation glove tip sampling takes place immediately following the completion of MFT, but before hand hygiene takes place. This testing is done to further certify the capability of staff members to ensure the safety and sterility of lab conditions.
Following the initial competency evaluation, the standard is to have glove tip testing done at least once every twelve months to make sure that employees are continuing to maintain training and safety procedures.
However, these guidelines fluctuate based on the risk level. In fluctuating conditions sampling may be recommended twice annually, or even more even often depending on the environment.
Additional testing is necessary to address the potential for failure. Frequent testing is the backbone of clean, sterile conditions, there to ensure that unforeseen circumstances don’t lead to prolonged corruption. The more often you test, the less likely prolific contamination will be.
Contamination at the microbial level can happen very easily. It’s important to understand that what 797 considers contamination might well be considered clean or sterile by other standards. Microbial contamination is dangerous partially for the fact that it isn’t visible to the naked eye.
Routine surface testing helps mitigate this risk by ensuring that you always know what, if any conditions are in your lab.
To make sure that testing is done properly, standardized guidelines are there to dictate how and what must be done. By following these standards, labs ensure that their definition of sterility is compliant with that established by USP 797.
For surface sampling results to be considered accurate and within the guidelines, the test must take place during a very specific time frame. Evaluations must occur at the very end of compounding activities, but before the area has been disinfected.
The idea here is to make sure that the surface test is evaluating the same conditions that took place during the processing and development.
PEC refers to the primary engineering controls—the equipment used to develop pharmaceuticals. Sampling the interior of this equipment is an important component of ensuring that ideal lab conditions are being met and maintained.
Similarly, it’s also important to take routine samples of the staging and work areas that are adjacent to the PEC. These stations are among the most touched places in the lab environment, making them a potential hotbed for contamination.
To that extent, any workstation or “frequently touched area,” should be considered a high priority for routine testing practices.
The current surface testing requirements indicate that tests should be done every six months at a minimum. This schedule keeps pharmacies compliant with regulations. However, businesses are free to test more often when they feel they are at higher risk for contamination, or they simply want to make sure that they are covering all of their bases.
Staying 797 compliant is key both to maintaining a safe and healthy work environment, and to making sure that unsafe medications aren’t doled out to the public. To maximize the safety of your lab setting, test as often as you feel is necessary.
When it comes to maintaining a compliant lab environment the stakes are pretty high. Remember that contamination can happen at the drop of a hat. When it does, you won’t usually know until after it is already too late.
The more vigilant you are with your testing and training procedures the better prepared you will be to maintain 797 standards.
Staying on top of employee training is one way you can help keep your lab environment safe. Train often and always make sure your staff understands the importance of guideline adherence.
Equally paramount, however, is to stay on top of your testing. Standards indicate annual glove tip testing, and twice annual surface testing to remain compliant. Pharmacies should, at minimum meet these guidelines.
However, you can always test more if you feel there is a risk of contamination, or if you just value being thorough.
Remember that having the right professionals on your side can make your testing procedures go smoother and more effectively.
Interested in Working with
Sure-BioChem Laboratories
Sure-BioChem Laboratories offers top-notch analytical testing for various industries. Our advanced lab and expert team ensure reliable, quality results. We're committed to excellence, helping clients meet high standards in environmental, food, and pharmaceutical testing.
Headquarters:
1000 Atlantic Avenue
Camden, NJ 08104
PHONE: 888-398-7247
Main Menu